Il existe aujourd'hui trois types de verre plat dans le monde : l'étirage à plat, le flottage et le calandrage. Le verre flotté, qui représente aujourd'hui plus de 90 % de la production totale de verre, est le matériau de base du verre architectural mondial. Le procédé de production du verre flotté, fondé en 1952, a établi la norme mondiale en matière de production de verre de haute qualité. Le procédé comprend cinq étapes principales :
● ingrédients
● fusion
● formage et revêtement
● recuit
● découpe et emballage
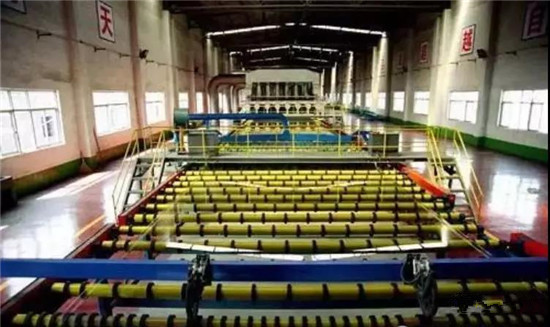
Ingrédients
Le dosage est la première étape qui prépare les matières premières pour la fusion. Ces matières premières, notamment le sable, la dolomie, le calcaire, le carbonate de sodium et la mirabilite, sont transportées par camion ou par train. Elles sont stockées dans la salle de dosage. La salle des matériaux est équipée de silos, de trémies, de convoyeurs à bande, de goulottes, de dépoussiéreurs et des systèmes de contrôle nécessaires pour contrôler le transport et le mélange des matières premières. Dès leur arrivée dans la salle des matériaux, les matières premières sont en mouvement constant.
Dans la salle de dosage, un long tapis roulant plat transporte en continu les matières premières des silos de matières premières vers l'élévateur à godets, couche par couche, puis les envoie vers la balance pour vérifier leur poids composite. Des fragments de verre recyclés ou des retours de ligne de production sont ajoutés à ces ingrédients. Chaque lot contient environ 10 à 30 % de verre brisé. Les matières sèches sont ajoutées au mélangeur et mélangées au lot. Le lot mélangé est ensuite acheminé de la salle de dosage vers le silo de tête de four pour stockage via le tapis roulant, puis introduit dans le four à un débit contrôlé par le doseur.

Composition typique du verre
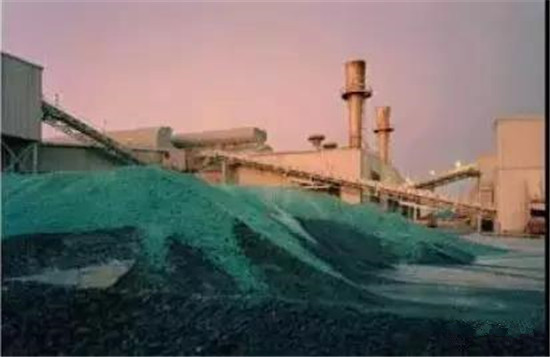
Parc à calcin
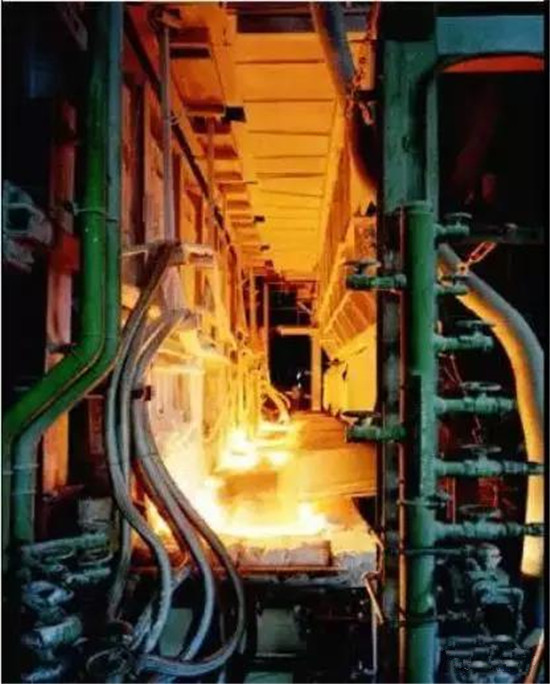
Introduire les matières premières mélangées dans l'entrée du four jusqu'à 1650 degrés avec une trémie
Fusion
Un four typique est un four à flamme transversale équipé de six régénérateurs, d'environ 25 mètres de large et 62 mètres de large, avec une capacité de production journalière de 500 tonnes. Les principaux éléments du four sont le bassin de fusion/clarificateur, le bassin de travail, le régénérateur et le petit four. Comme illustré à la figure 4, il est fabriqué en matériaux réfractaires spéciaux et possède une structure extérieure en acier. La charge est envoyée au bassin de fusion du four par l'alimentateur, qui est chauffé à 1650 °C par un pistolet de pulvérisation au gaz naturel.
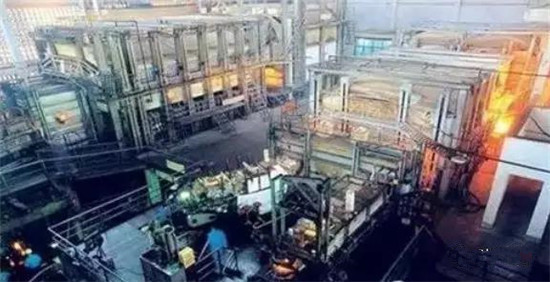
Le verre fondu s'écoule du bassin de fusion vers le col à travers le clarificateur et est agité uniformément. Il s'écoule ensuite dans la partie de travail et refroidit lentement jusqu'à environ 1 100 degrés pour atteindre la viscosité souhaitée avant d'atteindre le bain d'étain.
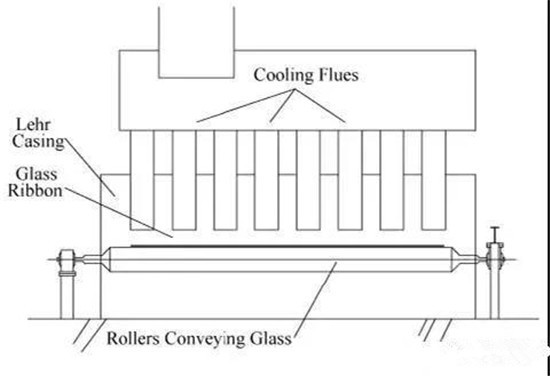
Formage et revêtement
Le procédé de transformation du verre liquide clarifié en plaque de verre est un procédé de manipulation mécanique qui respecte la tendance naturelle du matériau, dont l'épaisseur naturelle est de 6,88 mm. Le verre liquide s'écoule du four par le canal, contrôlé par une porte réglable, le piston, qui s'enfonce d'environ ± 0,15 mm dans le verre liquide. Il flotte sur l'étain en fusion, d'où son nom de verre flotté. Le verre et l'étain ne réagissent pas entre eux et peuvent être séparés ; leur résistance mutuelle sous forme moléculaire rend le verre plus lisse.
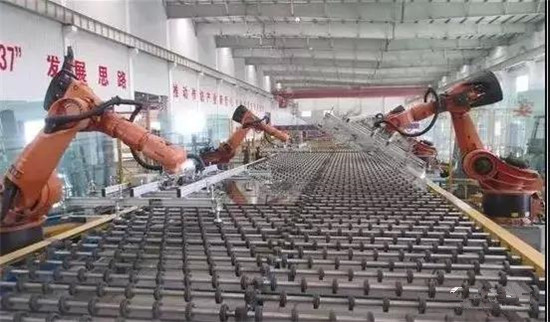
Le bain est une unité scellée sous atmosphère contrôlée d'azote et d'hydrogène. Il comprend un support en acier, des coques supérieure et inférieure, des réfractaires, de l'étain et des éléments chauffants, une atmosphère réductrice, des capteurs de température et un système de contrôle de processus informatisé. Il mesure environ 8 mètres de large et 60 mètres de long, et la ligne de production peut atteindre 25 mètres par minute. Le bain d'étain contient près de 200 tonnes d'étain pur, à une température moyenne de 800 °C. Lorsque le verre forme une fine couche à l'entrée du bain d'étain, on l'appelle plaque de verre. Une série de tire-bords réglables fonctionne de chaque côté. L'opérateur utilise un programme de contrôle pour régler la vitesse du four de recuit et de la machine à étirer les bords. L'épaisseur de la plaque de verre peut être comprise entre 0,55 et 25 mm. L'élément chauffant de la cloison supérieure permet de contrôler la température du verre. Au fur et à mesure que la plaque de verre circule dans le bain d'étain, sa température diminue progressivement, rendant le verre plat et parallèle. À ce stade, Acuracoat peut être utilisé pour le placage en ligne de films réfléchissants, à faible émissivité, de contrôle solaire, photovoltaïques et autonettoyants sur des équipements de pyrolyse CVD. Le verre est alors prêt à refroidir.
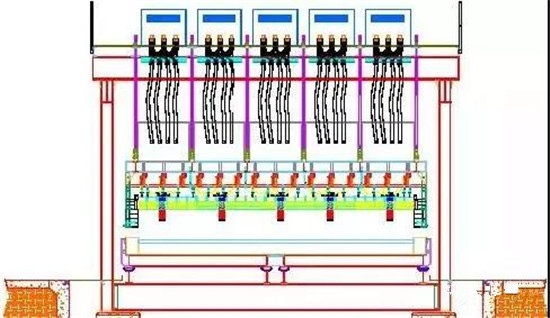
Coupe transversale de la baignoire
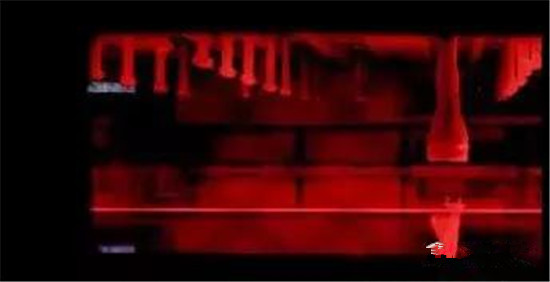
Le verre est étalé en une fine couche sur l'étain fondu, conservé séparément de l'étain et formé en une plaque
L'élément chauffant suspendu fournit un apport de chaleur, et la largeur et l'épaisseur du verre sont contrôlées par la vitesse et l'angle de l'extracteur de bord.
Recuit
Lorsque le verre formé quitte le bain d'étain, sa température est de 600 °C. Si la plaque de verre est refroidie à l'air libre, sa surface refroidira plus vite que son intérieur, ce qui entraînera une compression importante de la surface et des contraintes internes néfastes.
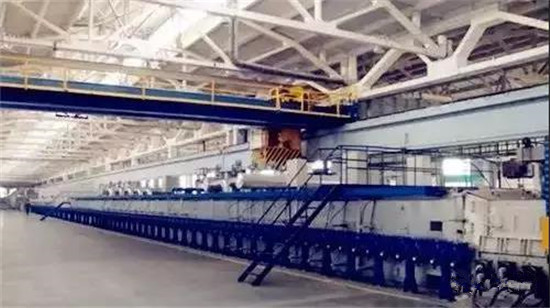
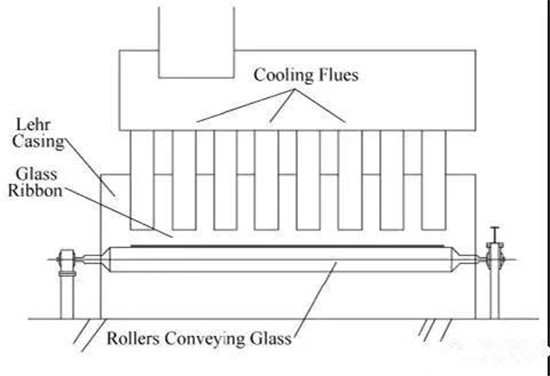
Section du four de recuit
Le chauffage du verre avant et après moulage entraîne également la formation de contraintes internes. Il est donc nécessaire de contrôler la chaleur pour ramener progressivement la température du verre à la température ambiante, c'est-à-dire le recuit. Ce dernier est réalisé dans un four à gradient de température préréglé (voir figure 7), d'environ 6 mètres de large et 120 mètres de long. Ce four est équipé d'éléments chauffants et de ventilateurs à commande électrique pour maintenir la stabilité de la répartition transversale de la température des plaques de verre.
Le résultat du processus de recuit est que le verre est soigneusement refroidi à température ambiante sans contrainte ni stress temporaire.
Découpe et emballage
Les plaques de verre refroidies par le four de recuit sont transportées vers la zone de découpe via la table à rouleaux reliée au système d'entraînement du four. Le verre passe par le système d'inspection en ligne pour éliminer tout défaut, puis est découpé à l'aide d'une meule diamantée pour éliminer les bords (les bords sont recyclés comme verre brisé). Le verre est ensuite découpé aux dimensions requises par le client. La surface du verre est saupoudrée de poudre, ce qui permet d'empiler et de stocker les plaques de verre sans risque de collage ni de rayures. Les plaques de verre impeccables sont ensuite empilées pour être emballées par des machines manuelles ou automatiques, puis transférées à l'entrepôt pour stockage ou expédition aux clients.
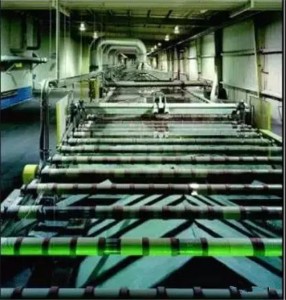
Une fois que la plaque de verre quitte le four de recuit, elle est entièrement formée et déplacée vers la zone de refroidissement pour continuer à réduire la température.